What Is Pvd Coating Physical Vapor Deposition Coatings Pdf Thin Pvd uses mainly physical processes to produce reactant species in the gas phase and to deposit films. in evaporation, source material is heated in high vacuum chamber. (p < 10 5 torr). mostly line of sight deposition since pressure is low. deposition rate is determined by emitted flux and by geometry of the target and wafer holder. Several methods are currently used for deposition of metal layers. advantages: highest purity (good for schottky contacts) due to low pressures. disadvantages: poor step coverage, forming alloys can be difficult, lower throughput due to low vacuum. evaporation is based on the concept that there exists a finite “vapor pressure” above any material.
Physical Vapor Deposition Pvd Methods For Synthesis Of Thin Films A ̈ load the source material to be deposited (evaporant) into the container (crucible) ̈ heat the source to high temperature ̈ source material evaporates ̈ evaporant vapor transports to and impinges on the surface of the substrate ̈ evaporant condenses on and is adsorbed by the surface. This updated version of the popular handbook further explains all aspects of physical vapor deposition (pvd) process technology from the characterizing and preparing the substrate material, through deposition processing and film characterization, to post deposition processing. Ture 6 pvd (physical v. por deposition): evaporatio. and. oration: ♦! the material to be evaporated. s heated in an evacuated chamber so that it attains a gaseous state. vapor. of t. is material traverse the space from the source to the substrate. ♦! typical deposition rates in industry is around 0.5 μm min (~8 nm s, for . Electron beam evaporation is a physical vapor deposition (pvd) technique known for having superior opportunities over deposition control rates, proper usage of material, and.

Pvd Physical Vapor Deposition Ture 6 pvd (physical v. por deposition): evaporatio. and. oration: ♦! the material to be evaporated. s heated in an evacuated chamber so that it attains a gaseous state. vapor. of t. is material traverse the space from the source to the substrate. ♦! typical deposition rates in industry is around 0.5 μm min (~8 nm s, for . Electron beam evaporation is a physical vapor deposition (pvd) technique known for having superior opportunities over deposition control rates, proper usage of material, and. We review the physical vapor deposition (pvd) techniques and equipment that are in common use in the high volume production of coatings that find application in the optical, display, decorative, tribological, and energy generating saving industries. Physical vapor deposition (pvd) includes vacuum evaporation, sputtering and ion plating. pvd pro cesses are used to apply functional hard coatings and decorative thin films. the most widely used coating is titanium nitride (tin). The book elucidates the crucial role of vacuum conditions, substrate temperature, and deposition parameters (pressure, power, deposition rate) in controlling film microstructure and properties. To form such reliable thin films of metals and later dielectric materials, two major methods of physical vapor deposition (pvd) are used: evaporation and sputtering. pvd processes use thermal and mechanical methods to coat samples, as opposed to chemical vapor deposition (cvd) processes, which rely on a chemical reaction to grow a film of material.
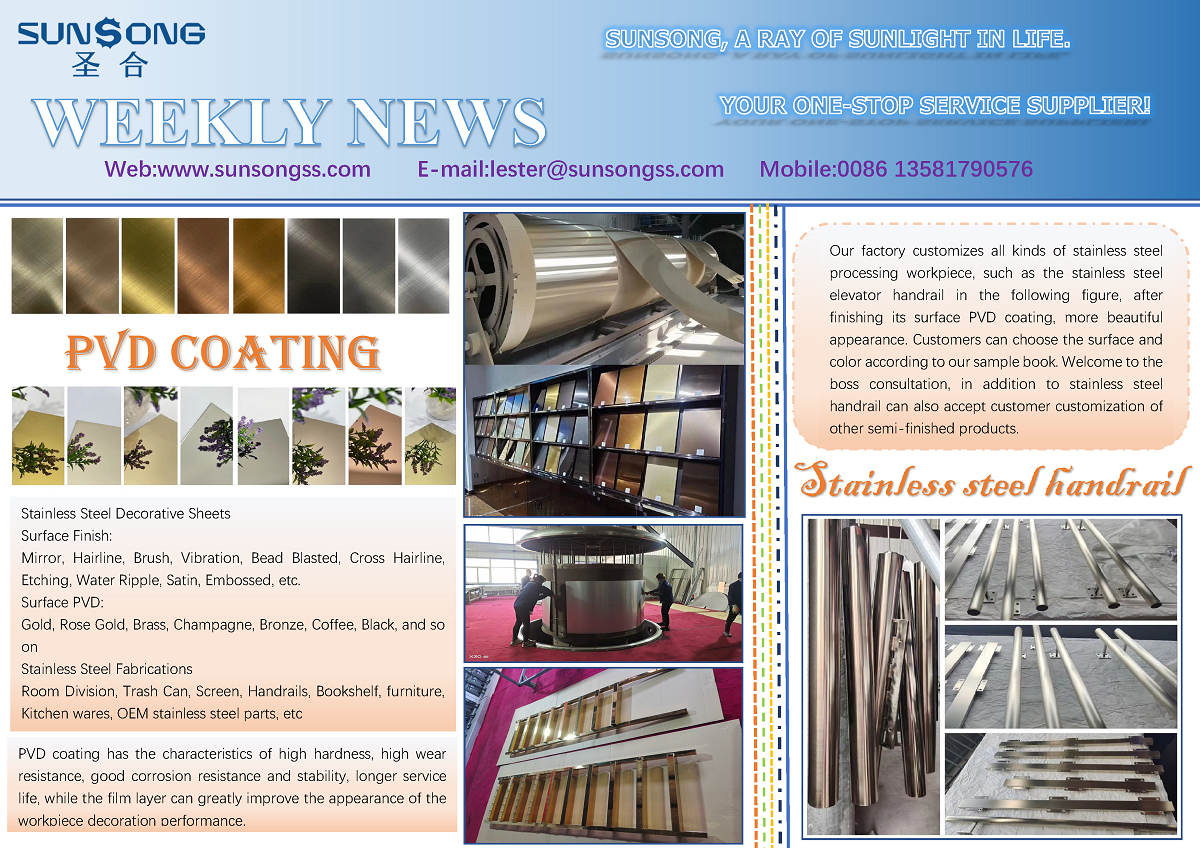
Pvd Physical Vapor Deposition We review the physical vapor deposition (pvd) techniques and equipment that are in common use in the high volume production of coatings that find application in the optical, display, decorative, tribological, and energy generating saving industries. Physical vapor deposition (pvd) includes vacuum evaporation, sputtering and ion plating. pvd pro cesses are used to apply functional hard coatings and decorative thin films. the most widely used coating is titanium nitride (tin). The book elucidates the crucial role of vacuum conditions, substrate temperature, and deposition parameters (pressure, power, deposition rate) in controlling film microstructure and properties. To form such reliable thin films of metals and later dielectric materials, two major methods of physical vapor deposition (pvd) are used: evaporation and sputtering. pvd processes use thermal and mechanical methods to coat samples, as opposed to chemical vapor deposition (cvd) processes, which rely on a chemical reaction to grow a film of material.

Physical Vapor Deposition Pvd Vacuum Deposition Methods Vaccoat The book elucidates the crucial role of vacuum conditions, substrate temperature, and deposition parameters (pressure, power, deposition rate) in controlling film microstructure and properties. To form such reliable thin films of metals and later dielectric materials, two major methods of physical vapor deposition (pvd) are used: evaporation and sputtering. pvd processes use thermal and mechanical methods to coat samples, as opposed to chemical vapor deposition (cvd) processes, which rely on a chemical reaction to grow a film of material.
Physical Vapor Deposition Pvd Pdf